​​Adoption of Modern Methods of Construction
Modern Methods of Construction (MMC) is a process which focuses on off-site manufacturing of homes (or significant parts of homes) as an alternative to traditional on-site construction methods.Â
The UK construction sector is in dire need of diversification and innovation, and MMC has the potential to deliver benefits such as:
-
Energy efficiency: volumetric homes have a much greater thermal efficiency due to the sealed membrane, with the manufacturing process offering greater quality and certainty, lowering bills and whole lifecycle carbon costs.
-
Lower build cost: advocates argue that at scale, MMC should reduce build costs by c. 20% versus traditional construction due to the efficiency of the manufacturing process and the ability to scale production easily.
-
Reduced maintenance costs: the uniform nature of MMC homes means that maintenance costs should be reduced for repairs, maintenance and upgradesÂ
-
Improved build quality: by manufacturing homes in a more controlled environment and having a repeatable process, quality control should be more achievable
-
More accessible, higher skilled jobs: a factory environment is more appealing and accessible, the digital processes that underpin MMC are more appealing to younger workers in an ageing sector and MMC workers can be drawn from the existing manufacturing workforce.
MMC has been a success story in many sectors like hotels, student accommodation, and education. In the first nine months of 2023, 22% of new build education projects included an off-site element. Despite these advantages, its adoption in the residential property sector remains limited, with only 10-15,000 homes delivered annually compared to the 75,000 homes per year goal set for 2030 by the 2021 Farmer Review.
The UK government has tried to encourage MMC adoption through targets, such as the Affordable Homes scheme, and financial support. However, these measures have not been sufficient to scale and stabilise the market, with high-profile failures like Urban Splash, Ilkley, and L&G Modular receiving significant press coverage, reducing confidence across the industry.
At TPXimpact we’re curious when we see challenges in the journey of a policy from intent to delivery of outcomes. Our Place and Infrastructure Practice have been using their networks and contacts to understand the on-the-ground barriers and untapped potential of MMC. For this rapid research, conducted over two weeks, we held semi-structured discovery interviews with 10 participants, including manufacturers, housing associations, local authorities, government organisations, and advocates. Alongside this, we analysed responses to the 2019 House of Commons inquiry into ‘What went wrong with MMC’, the House of Lords inquiry in 2024, a broad range of desk research, and analysis of performance data provided by research bodies and housing associations.
What are Modern Methods of Construction?
One of the challenges with MMC is its broad definition. It covers a range of approaches from fully offsite manufacturing to on-site process improvements. MHCLG introduced a seven-stage framework in 2017, detailing different grades of MMC:Â Â
-
Fully offsite volumetric housing (Category 1) - Entire, fully finished 3D modules (like complete rooms or sections of a building) are constructed in a factory and transported to the site. These modules are like giant, ready-made building blocks that are stacked and connected on-site to create the final structure.
-
Pre-manufacturing (Category 2) - Large flat panels, such as walls, floors, or roofs, are manufactured off-site and then transported to the building location. Think of this like assembling a giant jigsaw puzzle where all the pieces are pre-cut and ready to fit together.
-
On-site process improvements using off-site components (Categories 3-7) - These categories are pre-made non-structural parts like bathrooms and factory-made components, such as roof trusses, stairs, or windows, being delivered to a traditional site. They also cover on-site improvements such as 3D printing.
Categories 3-7 are more prevalent throughout the sector. But whilst they deliver some benefits, they do not provide the step-change promised by volumetric and pre-manufactured homes.Â
Systems and policy designÂ
From our research, we believe there is a key challenge to scaling, stabilising and embedding Category 1 and 2 MMC. This is the need to understand it’s an innovation (largely a manufacturing one) that sits within a wider system for how we plan, construct, finance, sell and manage homes. Our current system was largely designed in the 18th Century and is notoriously risk-averse, slow to innovate and characterised by labour and skills shortages. Unless we understand the broader systems in which MMC sits, the range of forces that act upon it and the different levers available to the government to influence it, it’s unlikely we’ll be able to deliver on its promises.Â
A policy design approach looking at the whole of the system in which MMC sits helps make sense of the different forces acting upon stakeholders and users. We can identify the major pain points which often occur at the intersection of different regulatory regimes, services and professions. It also allows us to think systematically about the different levers available to the government. These are distributed across regulators, funding agencies, industry bodies and arms length agencies, as well as the more direct policy and legislation available to central government. The Government as a System toolkit is a particularly useful framework to understand the different roles government can play in influencing change.
We’ve built up a high level picture of the system based on our research. From this, we identified four areas where better design of processes, legislation and policy could create the conditions that help increase the proportion of MMCs built in the market.
-
Financing and valuingÂ
-
Land use planning and Building control/inspections
-
Site professionals' awareness and capabilities
-
Insurance and warranties
Many other factors are at play in the system that seeks to deliver more MMC homes, which can be viewed in this high level systems map we rapidly designed.
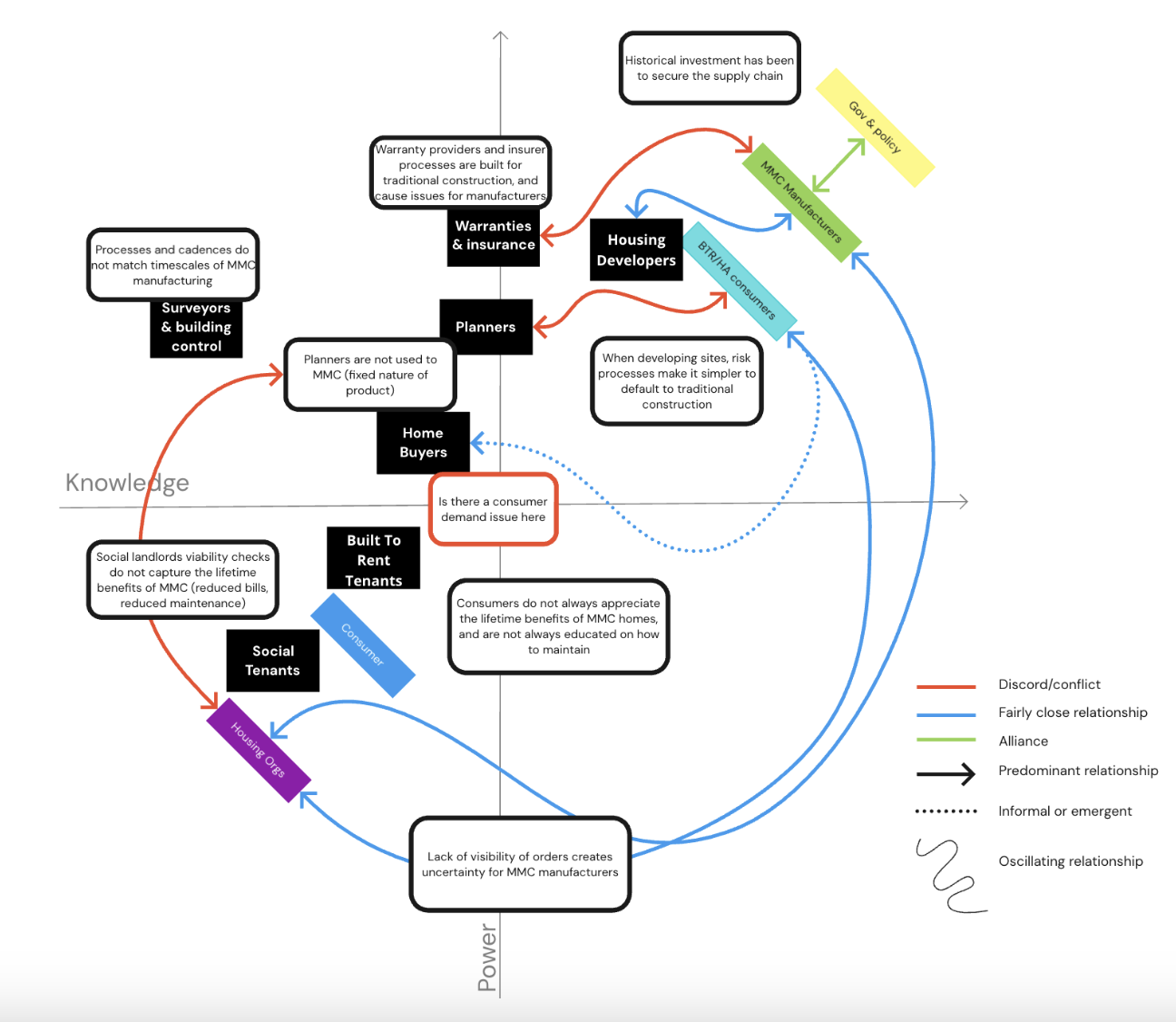
Financing and valuingÂ
MMC disrupts traditional for-sale house building viability models. Conventional homes incur costs over time, with sales from early phases financing subsequent construction. This gives flexibility for developers to slow down or speed up production if housing markets change. MMC requires significant upfront investment before a spade even hits the ground, tying up cash and reserves and creating the need to service debt for longer.Â
This creates financial and cultural barriers to choosing MMC over traditional construction approaches. Without full order books from housing associations, Build to Rent (BTR) providers or developers, factories struggle to achieve the scale necessary to reduce manufacturing costs - thus creating a further barrier.Â
Where the model is easier to embed is affordable housing and temporary accommodation where demand means rental income/returns are always guaranteed. Speed of construction means providers can increase their pace of affordable housing delivery, bringing in rental income and reducing the cost of ongoing maintenance.
Our research also uncovered evidence of aggregation of social housing demand beginning to happen. This gives manufacturers of Category 1 and 2 MMC housing greater visibility of future orders and should lead to higher factory utilisation and lower costs for the commissioning bodies.
Banks, lenders, developers and local authorities' current processes do not fully and accurately consider the lifetime benefits of potential properties ( carbon emissions, thermal efficiency savings, etc.). Nor does the process of valuing a home fully recognise its energy performance. Until the viability of MMC looks at the whole life costs it will be difficult to recognise the savings it brings/vs the current additional cost to deliver units.Â
Design opportunities
-
A role for the government in helping re-design the home buying and selling process for MMC, exploring how you enable mortgage valuations to recognise the whole life value of an MMC home and the role of professional bodies like RICs in supporting this approachÂ
-
Helping re-design systems and processes within local authorities and planning departments to internalise the positive externalities (e.g. reduced electricity bills, lower maintenance costs, reduced costs of homelessness and lower lifetime carbon emissions), will help for a fairer assessment of traditional versus MMC construction.Â
-
Continuing the digitisation of the planning system and creating data about design codes and patterns, to improve visibility of the MMC pipeline.
Land use planning and building control
The lack of certainty and slow and uneven progress of the planning system (no news to anyone!) is particularly challenging for MMC manufacturers and developers. At the macro level, MMC manufacturers want to produce as many homes, as fast as possible, so as to reduce the amount of stock and capital that they have to hold. The planning system is designed for traditional construction and development, meaning that pauses or hold-ups in the planning system are not that painful as developers can hold off buying materials or paying construction workers.
At the micro level, many authorities unwittingly have policies that are at odds with MMC or need careful consideration of how they can be incorporated into the MMC construction process (e.g. policies requiring the use of locally sourced building materials). There is often a lack of appreciation that small changes from planning officers can have a major impact on accreditation, delivery, timescales and cost.Â
Even when planning permission is granted, current building control and inspection regimes add further risk to MMC manufacturers. The process is designed around the piecemeal nature of construction of traditional homes, with the assumption that inspections should occur in a staggered manner and that key elements of the build like insulation need to be visible to the inspector on demand. This puts further grit into a manufacturing process that wants to move much faster than traditional construction, reducing efficiency gains and unpicking the design quality of the manufacturing process.
Design opportunities
-
Explore how national planning policy could incentivise greater consideration of MMC in the plan making process by Local Planning Authorities (LPAs)
-
Build on the national model design code by encouraging greater alignment of pattern books by MMC developers in local design codes - potentially endorsing certain patterns at a national level and supporting LPAs to share design codes that have been effective in delivery.
-
Designing shorter holistic inspection regimes for MMC homes, leveraging the existing factory quality assurance processes to drive time savings and better account for energy saving efficiencies.
Site professional's awareness and capabilities
A number of professions within the industry are rightly tasked with minimising risk to timescales, costs, delivery, and quality of the homes. As such, there are understandable concerns about employing unfamiliar methods to a site, which can lead to reversion to traditional methods.Â
A key point of risk for MMC is the literal interface with the ground, where it meets traditional construction skills, which have greater tolerances for error. In traditional construction, other trades can address a mistake or error made by the trade that came before it. In MMC the tolerance for errors is tiny - if there are errors in groundworks or foundations (which appear common) it causes delay and additional costs.Â
We need to educate the full suite of actors in the system of delivering a new MMC home to have the experience, skills and knowledge to work with it. Until that happens we’ll continue to see examples of site managers rejecting its use because they didn’t know how to store closed panel systems or don’t trust it as a construction system. The power and influence of these professionals (and their professional bodies) is a key area for government to use its soft power and influence (rather than policy and regulation) to improve awareness, upskill professions andÂ
Design opportunities
-
Acknowledge the difficulty and unlikelihood of changing the capability and perceptions of the current generation of site managers/leaders and invest in upskilling at source, by working with professional bodies (RTPI, RICS etc) in across the supply chain to embed knowledge and increase awareness of MMC in accredited courses at colleges and universities.Â
-
Encourage collaboration and innovation amongst those on the ground by creating a community of evangelists and innovators across local authorities, house builders, manufacturers and regulators (akin to the Open Digital Planning community) to inform policy, standards and services from the government.Â
Insurance and warrantiesÂ
The extensive periods of time it can take to obtain warranties, and the reticence of insurance providers to accept compliance with regulations, provide a further drag on delivery timescales. Market and consumer confidence, insurance and warranty legislation, and regulation and processes are still designed around traditionally built homes. There has been a nervousness to take risks due to limited evidence and data around performance, longevity and durability in this country (compared to the 100s of years of evidence on standard construction).Â
This challenge previously impacted mortgageability with lenders needing insurance on normal terms, a good warranty backing, and confidence there would be a resale market. We heard this challenge has lessened over the last five years as MMC manufacturers, and their consumers (Housing Associations, Build to Rent providers and housebuilders), work upfront with providers to build trust, confidence and knowledge of their products. The more experience lenders have of the properties, the more willing they are to lend, and the more easily and readily they do so.Â
Design opportunities
-
Build on existing good practices by encouraging working in the open and sharing knowledge of where and how insurance and warranty challenges have been overcome, seeking to bake this good practice into public procurement.
What next?
This short and sharp piece of research is not a substitute for full discovery with the support of government and industry. MMC is not a magic bullet to solving the housing crisis in the private housing sector. But it can be the solution to numerous challenges. In particular in policy design if it’s focused on increasing uptake amongst housing associations and built to rent providers, where the lean, quick and efficient processes of MMC best align.Â
It's also clear that the previous government initiatives such as the financial support provided at the macro scale by Homes England have not brought about change. Without fully understanding the incentives and processes involved at a micro level limiting the adoption at site level, it is difficult to best design how different government levers (across different departments and arms length bodies) can be used to address these issues at the policy, funding and regulation level.  Â
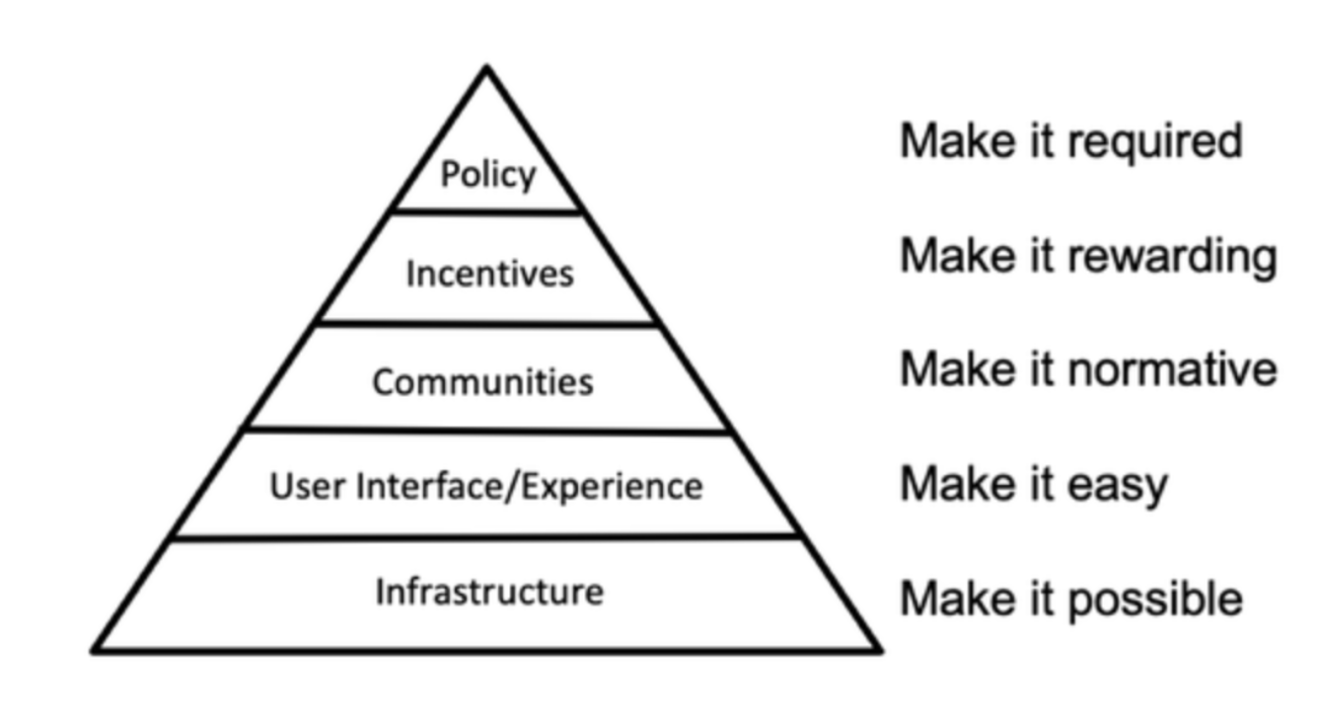
The Centre for Open Science’s framework for bringing about cultural change in science provides a useful way of thinking about how the government can support the scaling of MMC. Critically it asserts that the pyramid is progressive; success towards the pinnacle of the pyramid requires successful implementation at the lower levels. Policy is only successful if incentives, communities, experiences and infrastructure are in place to support that policy., Previous attempts to scale MMC via policy and funding forgot to make MMC normative, easy and possible.
There is still a lot of research required to fully understand these challenges, but we believe that this is a systems problem that will require a systems solution. Successful delivery of MMC sites and dissemination of the benefits for developers, consumers, and (for social homes) local authorities will encourage further developments. It is the role of the government to help convene this approach and help the sector get out of its own way to help deliver meaningful change.Â
Our recent insights
Transformation is for everyone. We love sharing our thoughts, approaches, learning and research all gained from the work we do.
-
-
NHS Ten Year Plan review
Read insight -
How AI can reinvent the foundations of planning
Read insight -